Micro Lab
The MHS Micro Lab specializes in micro-injection molding of miniature, high-precision plastic parts for industrial applications. Featuring state-of-the-art M3 micro molding machines and post-molding inspection equipment, the Micro Lab serves as a testing facility for our global customer base, where every detail of a project is examined and validated in a scientific, systematic way.
Micron Precision
The average human hair is approximately 100 microns thick. MHS micro molds and cavity features are measured in micron accuracy and have a tolerance of < 10 µm. From micro cavities and mold components to downstream part handling and automation, everything has to be perfect. While mold replication and process repeatability are of the utmost importance to achieve sound mechanical and optical parts, we take testing to a new level by investigating the behaviour of the melt before, during and after molding, in order to provide empirical data that your part does in fact achieve the intended material integrity and functions as designed, in the real world.
Advanced Testing
Micro parts can’t be tested and analyzed the same way as larger plastic parts so in order to guarantee a perfect part, it is necessary to drill down to the molecular level. TGA (Thermogravimetric Analysis) and DSC (Differential Scanning Calorimetry) testing help us analyze material properties by measuring weight loss due to thermal degradation (TGA) and heat flow changes related to phase transitions, crystallization, and thermal stability (DSC). After billions of cycles, we have learned that the proprietary ISOKOR™ injection process, featured in M3 molding machines, improves the internal structure of each part by ‘packing’ the melt at the final stages of injection.
Mold Trials
The M3 micro-injection molding machine from MHS seamlessly bridges the gap between prototype molding and high-volume production. Its precise control over temperature, pressure, and injection speed ensures consistent part quality, even in small quantities. With its ability to handle complex, intricate designs at micron-level precision, the M3 is ideal for prototyping. As design validation progresses, the machine’s repeatability and scalability enable a smooth transition to high-volume production without sacrificing quality or performance. This flexibility reduces development time and cost, allowing manufacturers to efficiently scale production while maintaining consistent part integrity.
Better Micro Parts
The patented ISOKOR™ process that powers the M3, recognizes that the extremely small mold cavity volume of a micro-part must fill with melt in only a few milliseconds. The smaller the part volume, the less thermal energy or heat capacity the melt contains. Thermoplastic materials differ widely in enthalpy. For example, HDPE has double the enthalpy of PET or PBT. This must be considered for the cavity-flow- distance in addition to wall thickness, viscosity, shear rate, temperature and pressure. Melt with a fast solidification like LCP, PEEK, PA, POM for parts with micro-features and thin walls requires a high fill velocity and no fill-front hesitations. The traditional screw or screw/plunger injection approach for micro-parts is too slow and inaccurate. The conventional system starts from zero melt pressure, and while the pressure increases to peak pressure, the melt density changes. The melt metering cushion plus the melt volume in the hot runner melt distribution channels absorbs up to 15% of the injection metering stroke. In high cavitation molds, the amount of volumetric compression often exceeds the volume of the micro-part itself. The M3 solves this issue.
“At MHS we are dedicated to creating a new gold standard in micro injection molding by using all the scientific methods available to ensure your part is 100% reliable.”
Harald Schmidt - VP Engineering
Inspection
In addition to material testing, CT scanners are used in-house to inspect micro-sized injection-molded parts, offering a non-destructive method to analyze internal and external structures with high precision. By generating detailed 3D images, CT scanning allows engineers to detect defects like voids, cracks, or inconsistencies in complex geometries that may not be visible externally. This technology is particularly valuable for micro-molded parts, where traditional inspection methods may struggle to provide accurate results. CT scanning enhances quality control by providing in-depth insight into the part’s integrity, ensuring that it meets tight tolerances and performance standards before moving to production.
Analysis
Our team of hot runner experts utilizes the latest analysis software. These tools play a critical role in micro-injection molding by optimizing process parameters and ensuring part quality. Flow analysis predicts how molten polymer fills micro-cavities, identifying risks like short shots or air traps. More importantly, density and frozen layer formation analysis help refine processing conditions. Density simulation ensures uniform material distribution, reducing defects like voids or sink marks. Frozen layer analysis models how polymer solidifies, optimizing cooling rates to prevent premature solidification or weld line weaknesses. These simulations enhance precision, minimize waste, and ensure high repeatability—essential for micro-molded medical and high-performance components with strict dimensional tolerances.
Optimization
Produce millions, even billions, of parts without waste, and with perfect replication. Imagine new possibilities! As ISOKOR technology redefines the cutting-edge standard of what’s possible, part designers will be able to create innovative new micro components never before dreamed of. At MHS we have always believed that everything starts and ends with the part. It is the unifying goal that ties all the decision makers together - end users, OEMs, molders, mold makers, and hot runner teams. That is why we strive to live by our make better parts philosophy. We guarantee you won’t find a more expert team anywhere else. Every part has a story. What’s yours?
Applied
Polymer Science
The future of manufacturing requires micro injection molded parts made from a growing list of specialized materials. The M3 makes it possible to mold a wide selection of plastics, from advanced engineering resins to extrudable non-polymers. The possibilities are endless.
Improved Morphology
in Micro Parts
The ISOKOR™ process ignores volumetric metering altogether. The focus is on maintaining a constant melt pre-compression in front of the screw and throughout the entire hot runner system. The increased melt density keeps the molecules condensed and compression-charged with elastic energy. When the valve gate opens to fill the micro-cavity, part of this energy expands to fill the cavity within milliseconds. The emphasis of this expansion process is on the speed at which the cavity fills. The faster the cavity fill time (occurring in less than 10 milliseconds), the shorter the duration in which the melt is in contact with the walls of the micro-cavity. This slows down the formation of a frozen layer while the melt fills the cavity. The primary function of the manifold-integrated injection plunger is to pre-pressurize the melt to a controlled peak pressure plateau. The plunger motion reaches an equilibrium between melt compression and plunger force. When the valve gate has opened and melt has filled and pressurized the cavity, the plunger continues with a second motion to instantly recover from the pressure drop caused by the expansion. This way, the plunger motion rebuilds a second melt pressure plateau in the system to establish a new equilibrium. With the plunger reaching the second pressure plateau, the valve gate closes.
The faster the injection velocity reaches a high melt pressure inside the micro-cavity, the less time it takes for the material to solidify. This physical phenomenon is called cooling with pressure. The high cavity pressure that is generated by the valve pin closing motion, leads to a final peak pressure in the micro- cavity and the solidification temperature or transition temperature shifts to a higher temperature value. Consequently, the micro-part achieves higher material density, better cavity replication, less shrinkage and a faster cycle time. The ISOKOR™ micro molding process provides more tha 10 times faster melt injection velocity. That high speed is particularly important to address the low enthalpy of micro-parts below 100 mg, or even 10 mg.
Material Integrity
It’s not enough to visually inspect a part using a microscope or even a CT scanner because it doesn’t tell the complete story. To know if a micro part is good, it is critical to look inside the plastic. TGA and DSC material testing can help identify plastic degradation in a micro-molding application by detecting changes in thermal stability and molecular structure. TGA monitors weight loss due to thermal breakdown, while DSC measures heat flow to reveal any shifts in the plastic’s crystallization or phase transitions, both of which indicate potential degradation that could affect the final part quality. By taking samples from the hopper, the melt channel and the solid molded part, it is possible to scientifically prove that the integrity of the material is not only maintained but improves during the ISOKOR™ injection process due to the added density created during high-speed injection and cooling.
The M3 micro molding machine by MHS is a high-precision, fully automated injection molding system designed for ultra-small, high-tolerance parts. Utilizing ISOKOR™ technology, it ensures consistent shot-to-shot quality with a cleanroom-ready, all-electric platform. The M3 excels in multi-cavity production with zero material waste, making it ideal for medical, electronics, and micro-optics applications. Its servo-driven, high-speed injection system delivers unmatched repeatability, while its modular design supports rapid mold changes, enhancing efficiency for demanding micro-molding projects.
Micro Molds
Micro Molding FAQ
-
Micro injection molding is a specialized manufacturing process used to produce extremely small and precise plastic components, often with complex geometries and tight tolerances. It is commonly used in industries such as medical, electronics, and micro-mechanics, where parts can weigh as little as a fraction of a gram and have intricate features down to the micrometer scale. MHS defines micro molding by referring to direct-gated plastic parts weighing under 200 mg.
This process typically involves high-precision micro injection molding machines, such as the MHS M3, which are designed to handle very small shot sizes, precise material dosing, and controlled cavity filling. Factors like material selection, mold design, and processing parameters are critical to achieving high repeatability, minimal waste, and optimal part integrity in micro injection molding.
-
How do you measure the quality of a micro-injection molded plastic part?
Through extensive research and testing, we’ve discovered that the only way to achieve perfect part quality in micro molding is through the use of direct-gating using a specialized valve gate hot runner system like the M3 with its patented ISOKOR process. There are four main factors that determine the form and function of the part, or the internal and external structural characteristics:
1. Compressibility of the melt
2. Melt residence time
3. Injection velocity
4. Ratio between part volume and surface
Inspecting the outer dimensions of the micro part, no matter how precise, does not provide a full analysis of the internal quality of the material post-molding. Only scientific lab testing like DSC and TGA can guarantee perfect part properties.
-
How do you produce large quantities of micro parts?
Scaling micro-injection molding requires a combination of high-cavitation tooling, automation, and efficient process control. Key strategies include:
• Multi-cavity molds (4, 8, 16, or more) to increase part output per cycle.
• Lights-out manufacturing: Automated systems allow 24/7 production.
• Workcell configurations with multiple M3 machines running simultaneously.
• In-mold automation: Integrated pick-and-place robots for fast part handling.
• Standardized mold bases to reduce tool changeover time.
-
What materials can micro molded plastic parts be made from?
Micro-injection molding works with high-performance thermoplastics, including:
• Engineering plastics: PEEK, LCP, PPS, PBT (for high heat resistance).
• Medical-grade plastics: Bioabsorbable materials (PLA, PGA, PCL), PEEK, PEI (for implants).
• Elastomers: TPE, LSR (for soft micro components).
• Conductive & specialty materials: Carbon-filled plastics, ESD-safe compounds.
-
How do you design a part for micro-injection molding?
Designing for micro-molding follows DFM (Design for Manufacturability) principles:
• Wall thickness vs flow length ratio (consider low material enthalpy)
• Draft angles: At least 1-2° for easy ejection.
• Micro features: Consider tolerances down to ±5 microns.
• Gating strategy: Use direct gating (hot runners) to eliminate waste. Cold runners and sub-runners dramatically reduce the accuracy of precise injection parameters and should be avoided, if possible.
• Material flow: Optimize for low melt shear and pressure drop. Flow analysis can be used to simulate the cavity fill conditions prior to mold manufacturing. Only certain types of software can produce the special high-velocity conditions needed to fill the part at millisecond speeds.
-
What special requirements do you need to consider when manufacturing micro-injection molds?
Tooling considerations for micro-injection molds include:
• High-precision machining: EDM, micro-milling, and laser machining for intricate details.
• Polishing & surface finish: Ultra-smooth surfaces to reduce sticking.
• Material selection: Hardened tool steels (PM powder metallurgic with fine alloy dispersion e.g. Mo, W, Cr, Ni) for durability.
• Venting: Micron-level venting to create a cavity vacuum prior to injection.
• Uniform mold temperature: For high temperature materials like PEEK and LCP of up to 200 degrees Celsius (400 Fahrenheit).
• To avoid flash on your micro part, the accuracy of the mold parting line and mating inserts and components (slides, cores, ejector pins/sleeves), extreme machining tolerances are required in order to achieve micro-gaps in the micron range.
-
How do you manufacture prototype micro parts?
The only way to produce prototype plastic parts in the micro range that accurately represent the characteristics of the finished product, is to injection mold them. This requires a prototype mold.
Machines like the M3-D08 micro-injection molding machine effortlessly transition from prototype molding to high-volume production. Their precise control over temperature, pressure, and injection speed ensures consistent quality, even for small production runs. The M3 excels at handling intricate, complex designs, making it ideal for prototyping. Its repeatability and scalability support a seamless shift to high-volume manufacturing without compromising quality or performance. This adaptability streamlines development, reduces costs, and enables manufacturers to scale efficiently while maintaining exceptional part integrity. Validation processes like FDA approval are simplified, as the processing parameters and equipment used to produce the parts remains consistent in both the prototyping and the serial production phases of your project.
-
What methods are available to test the quality of micro plastic parts?
Micro parts require advanced metrology & inspection techniques:
• Optical microscopy: High-magnification inspection for surface defects.
• Micro CT scanning: 3D internal defect analysis.
• CMM (Coordinate Measuring Machine): Sub-micron accuracy for dimension checks.
• X-ray fluorescence (XRF): Material composition analysis.
• DSC (Differential Scanning Calorimetry): Measures heat flow changes related to phase transitions, crystallization, and thermal stability
• TGA (Thermogravimetric Analysis): Analyzes material properties by measuring weight loss due to thermal degradation
-
How do you control the special molding parameters in micro part production?
Micro-molding relies on precise control of injection speed, pressure, and temperature:
• Shot size accuracy: As low as 0.1 mg per shot.
• Injection velocity: Ultra-fast speeds prevent premature cooling.
• Closed-loop monitoring: Real-time adjustments ensure consistency.
• Temperature control: Strictly regulated within ±0.5°C. Micro parts are typically molded at elevated mold temperatures to accommodate perfect surface replication and cavity fill
-
How are micro-molded parts best handled after injection?
Due to their small size, micro parts must be handled carefully to avoid loss or damage:
• Static-free trays: Prevent electrostatic attraction.
• Automated sorting: Vision-guided robotic systems.
• Micro vacuum pickup tools: For delicate handling.
• Automated conveyors: Reduce contamination risk.
What specialized automation equipment is needed to process micro parts downstream, post-molding?
• Robotic handling systems: Microscopic pick-and-place robots.
• Automated quality inspection: Inline vision systems.
• Laser marking: Permanent identification.
• Automated packaging: Precision feeding systems for sorting & bagging.
How can micro-sized plastic parts be assembled, if required?
Micro part assembly often uses:
• Micro ultrasonic welding: For tight, seamless joins.
• Laser welding: High precision for medical & electronic components.
• Adhesive bonding: Using micro-dispensing systems.
• Micro press-fitting: For snap-fit designs.
-
What are some packaging options for miniature plastic components?
• Tape-and-reel: For electronics & automated assembly.
• Blister packs: Individual component packaging.
• Vacuum-sealed trays: For high-value medical parts.
• Bulk packaging: Static-free bags or vials for general-use parts.
-
What are typical applications or industries in which micro parts can be employed?
Micro-injection molded parts are used in:
• Medical devices: Microfluidics (lab-on-chip), Catheter tips, implantable devices, surgical tools.
• Electronics: Micro-connectors, LED components, sensor housings, lenses and optics
• Automotive: Micro gears, fuel system components, sensors.
• Consumer products: Hearing aids, watch components.
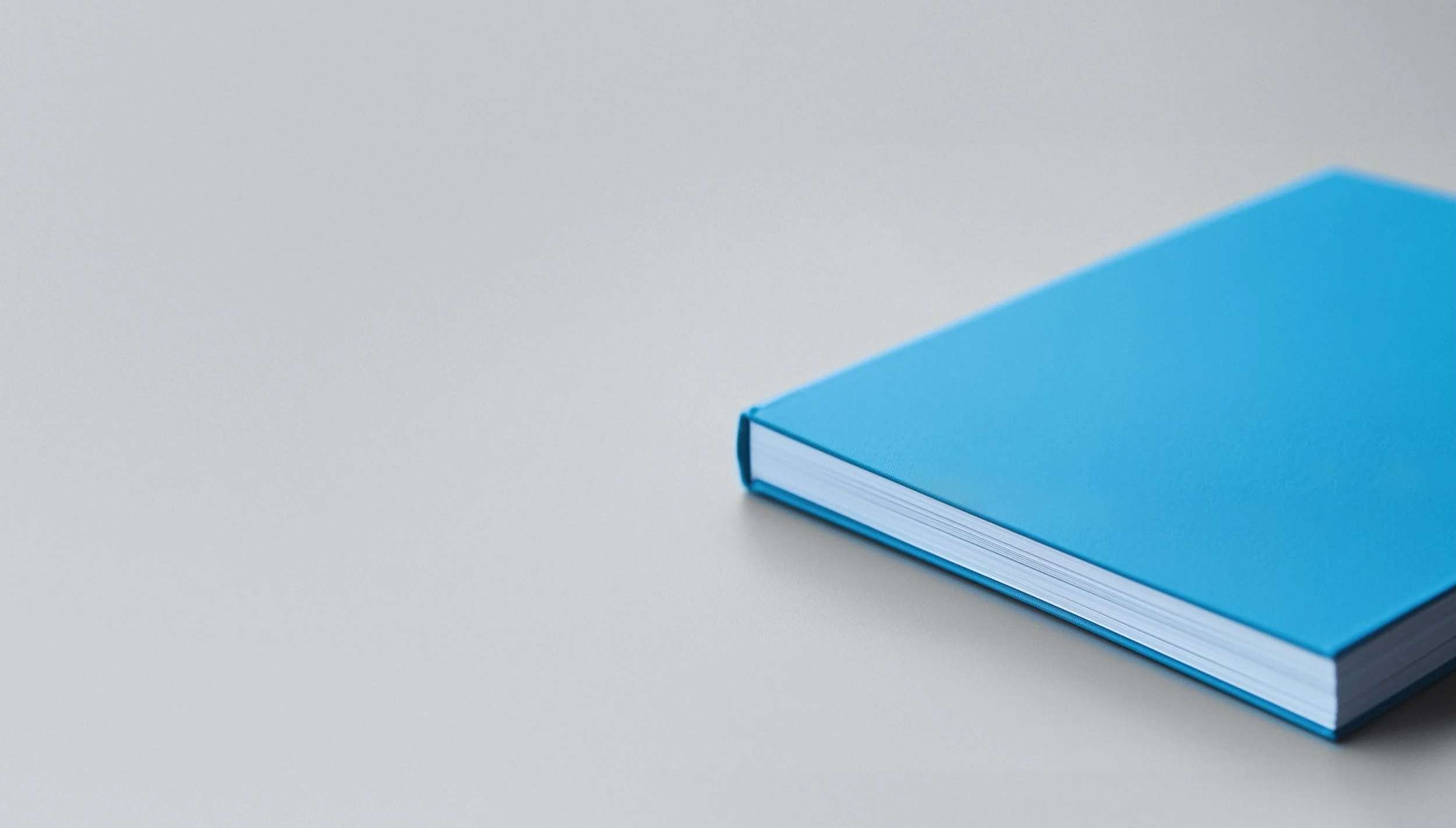
White Paper
Advancements in
Micro Molding 2025
Ready to start?
Take a minute to share your project details with us and we’ll explore the best options for your micro-injection molded part.